CS3252 Management Science
Tutorial # 10, October 12 - October 17, 1998
- Barbara Tan is the purchasing agent for West Valve Co. The company
sells industrial valves and fluid control devices. One of the most popular
valves is the Western, which has an annual demand of 4000 units. The cost of
each valve is $90 and the inventory carrying cost is estimated to be 10%
of the cost of each valve. Barbara has made a study of the costs involved
in placing an order for any of the valves that the company stocks, and she has
concluded that the average ordering cost is $25 per order. Furthermore,
it takes about two weeks for an order to arrive from the supplier.
- What is the economic order quantity?
- What is the reorder point?
- What is the total annual holding cost?
- What is the optimal number of orders per year?
- What is the optimal number of days between any two orders?
- Jan Gentry is the owner of a small company that produces electric
scissors to cut fabric. The annual demand is for 8000 scissors, and Jan
produces the scissors in batches. On the average, Jan can produce 150
scissors per day and during the production process, demand for scissors has
been about 40 scissors per day. The cost to set up the production process is
$100, and it costs Jan 30 cents to carry one pair of scissors for one year.
How many scissors should Jan produce in each batch?
- Sarawak Products offers the following discount schedule for its
four-by-eight foot sheets of quality plywood:
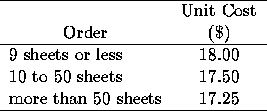
Home Sweet Home Company orders plywood from Sarawak Products.
Home Sweet Home Company has an ordering cost of $45. The carrying cost is
20%, and the annual demand is 100 sheets. What do you recommend?
- Linda Lim is in charge of maintaining hospital supplies at Kandang
Kambing Hospital. During the last year, the mean lead time demand for bandage
BX-5 was 60. Furthermore, the standard deviation for BX was 7. Ms. Lim
would like to maintain a 95% service level.
Linda knows that the carrying cost of BX-5 is 50 cents per unit per year.
What safety stock level do you
recommend for BX-5? Compute the holding cost of the safety stock.
- Creative Coffee sells an average of 200000 pounds of roasted coffee beans
each year to supermarkets with standard deviation of 25238.85 pounds.
The company's importer charges $1 per pound plus $300 per
order. Once an order is placed, it takes 4 weeks for Creative's South
American partner to roast the beans, clear them through customs, and got them
to Creative's plant. An additional $50 covers the clerical and other costs
associated with placing an order. The annual carrying rate is 25%
per year. Management wants to achieve a service level of 90% with a periodic
review policy every 2 weeks.
Compute
- The mean and standard deviation of the demand during the review period
of T = 2 weeks plus the lead time of L = 4 weeks.
- The amount of safety stock and the ordering policy to achieve the given
service level.
- The total annual cost of the optimal inventory policy.
RUDY SETIONO
Thu Oct 1 09:37:01 SST 1998